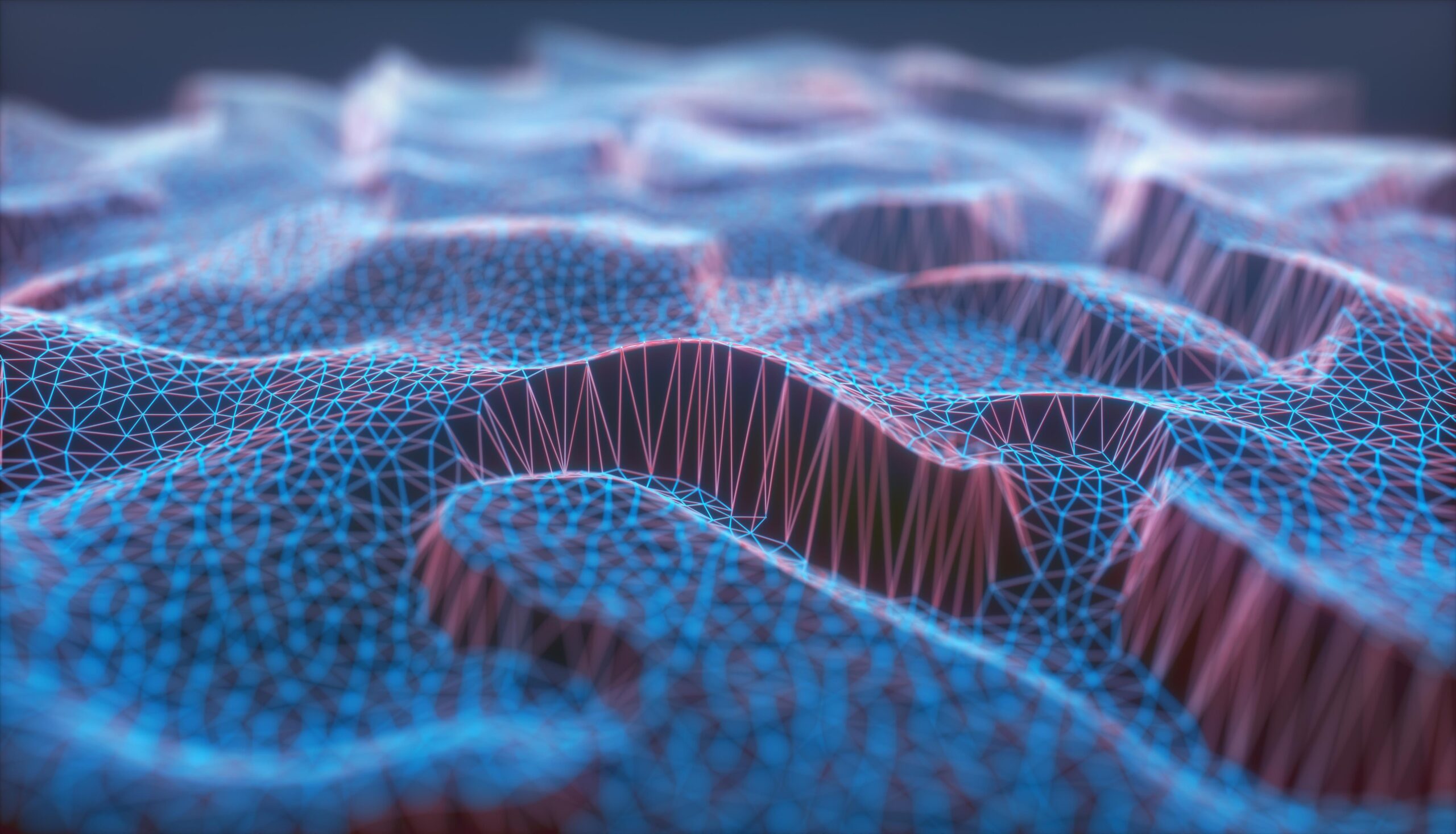
Nearly a century after it was first developed, polyethylene terephthalate (PET) plastic — recognizable by its #1 recycling symbol — is one of the world’s most ubiquitous materials. Used in everything from synthetic textiles and packaging to food and beverage containers, more than 55 million tons of PET are produced every year. Despite its widespread prevalence, consumers and businesses are increasingly looking for sustainable alternatives, as the negative impacts of petroleum-derived plastics become more widespread.
An increasingly promising substitute is polyethylene furanoate (PEF), a bio-based plastic with nearly identical properties to PET but a much smaller environmental footprint. They may look and feel pretty much the same, but at the core of PET and PEF lie markedly different inputs.
PET production utilizes crude oil, which is broken down and then processed into terephthalic acid (the final precursor). PEF on the other hand, forgoes fossil fuel inputs in place of hydroxymethyl furfural (HMF), a type of renewable biomass derived from natural sugars. Once refined into furandicarboxylic acid (FDCA) — the bioequivalent of terephthalic acid — the compound is ready to make PEF.
The molecular composition of PET and PEF are extremely similar, but because of different feedstocks — renewable biomass as opposed to crude oil — PEF is vastly more sustainable. In fact, PEF can reduce relative lifecycle emissions by more than 75%, providing an efficient means of reducing the industry’s roughly 26 million tons of annual CO2 emissions. As an added benefit, PEF-based products are far easier to recycle, helping improve the circularity of the plastics economy.
The advantages of PEF don’t end with sustainability. On an industrial scale, PEF production can actually be more cost-competitive than PET, a remarkable feat considering the industry’s nascency. PEF also exhibits superior performance characteristics, including a more durable gas and moisture barrier which helps sealed items (i.e. food and beverage) stay fresh for longer. PEF is preferable from a manufacturing standpoint, boasting a higher glass transition temperature, a lower melting point, and higher tensile strength. This combination of qualities make PEF a choice replacement for PET, as it’s both uniquely scalable and high-performance.
Despite this, PEF made up less than 1% of the 370+ million tons of plastic produced in 2022, an issue that can largely be attributed to downstream manufacturing inefficiency. The majority of PEF production today relies on outdated chemical or thermal methods to convert HMF into FDCA (the precursor to PEF). These techniques lead to high energy costs and greater carbon emissions, ultimately rendering the would-be benefits of bio-based PEF moot.
The solution to scaling PEF lies with a new production method — electrochemical oxidation — which is vastly more efficient and cost-effective at converting HMF into FDCA. This approach offers several advantages, including the ability to run at ambient as opposed to elevated temperatures and pressures, minimizing energy use and reducing costs by up to 25%. Electrochemical oxidation also eliminates the need for costly catalyst materials. Importantly, green hydrogen is produced alongside FDCA through a coupled reduction in the same reactor, allowing manufacturers to increase their productive capacities and profits. Despite its vast potential, however, electrochemistry has been unable to deliver on the promise of commercially viable PEF to date.
Mattiq is pushing electrochemical PEF production forward by tackling the industry’s longest-standing challenges, from intra-industry fragmentation and compartmentalization to inefficient system optimization. Electrochemical process development has historically been slow, but through a uniquely staged approach, Mattiq is changing this.
Utilizing parallel experimentation techniques that replicate and miniaturize industrial processes, Mattiq’s electrochemical system development and optimization is opening new opportunities for collaborative ecosystem formations and commercially viable electrochemical PEF pathways.
Scaling the production of PEF represents a pivotal step towards decarbonizing consumer plastics, and by harnessing the power of advanced electrochemistry, Mattiq is paving the way there.
Learn more about our approach and solutions: mattiq.com/solutions